For about 25 years, the basic ideas and core principles of the Toyota Production System (TPS), developed in the 1950s, have been omnipresent in trade, service, and industrial companies. The Lean Management promoted and implemented there has long since evolved into an important management discipline. With the vision of Lean Industry 4.0, it is now gaining even more current relevance. Classic project management has also undergone a transformation within the scope of Lean Project Management. In the following article, you will learn everything you need to know about Lean Project Management, including its core principles, techniques, tools, and objectives.Â
What is Lean Project Management?
Minimizing waste, increasing productivity, focusing on the essentials, and thereby driving the efficient design of the entire value chain – these are the three core themes of Lean Management. The term Lean Management can be translated as “slim management.”Â
Overall, it primarily involves measures for continuous process optimization. This comparatively young form of management is based on five core principles. Which these are exactly, you will learn later in this article.Â
KEY POINTS
- Lean Project Management focuses on minimizing waste and maximizing customer value.
- By applying Lean principles, processes and projects are designed to be more efficient, value-oriented, and profitable.
- The core of Lean Management is the continuous pursuit of perfection to constantly improve product and service quality.
What Are the Differences From Traditional Project Management?
The Lean principles established within Lean Management can also be applied in project management. The focus here is primarily on two aspects: minimizing waste and creating added value for the customer. By applying these principles or practices, you can ideally reduce all types of waste.Â
This can make processes and projects more predictable, efficient, value-oriented, sustainable, and ultimately more profitable. Furthermore, Lean Management or Lean Project Management aims to significantly improve the productivity of all relevant production factors and product quality.Â
How Did the Discipline of Lean Project Management Develop?
Lean Management and its corresponding functions and measures have their historical origins in Japan. In the 1950s, Taiichi Ohno, the then production manager at Toyota, developed a principle that placed the individual workplace at the center and perfectly aligned various processes. This new production approach considered not only the technical processes but all activities and processes within the company. This holistic perspective aimed at establishing a stable quality level and continuously optimizing the entire value chain.Â
What Are Advantages of Lean Project Management?
- Minimizes wasteful factors and measures
- Optimizes inventory required by the project team
- Eliminates unnecessary bureaucracy and processes
- Organizes projects and processes more efficientlyÂ
- Reduces error rates in project and process flowsÂ
- Improves product and service qualityÂ
- Reduces costsÂ
- Increases customer satisfactionÂ
However, you should always consider that you cannot apply Lean Management template-like to every single area. For instance, implementing Lean activities in project management requires various adaptations. The basis, however, always remains the Lean principles developed by Taiichi Ohno.Â

Find qualified Project Manager!
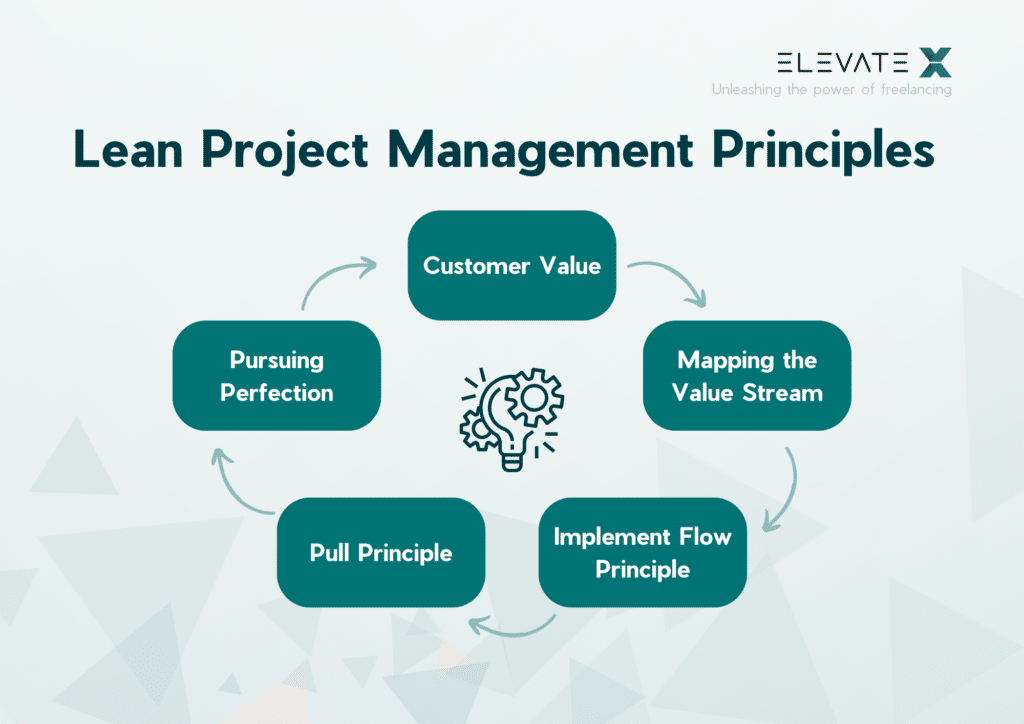
Five Core Principles of Lean Management
1. Customer Value - Keeping the Benefits from the Customer's Perspective in Mind
The focus of the Lean concept should always be on the customer. In this regard, the product value must always be defined and identified from the customer’s perspective. It is important to consider that products and services are usually dependent on a variety of customer relationships. This means: In addition to focusing on the end customer, the entire customer chain must be taken into account. What is important here is what the respective customer defines as value. Thus, the maximum orientation towards the customer is the core. The goal is to meet all the customer’s requirements.Â
2. Identify the Value Stream - Focusing on Value-Adding and Value-Diminishing Activities
The second core principle focuses on identifying the value stream. The value stream includes all project and work steps that are actually necessary for product manufacturing or the provision of an agreed service. To identify the value stream, all activities must be identified and recorded. Then, you evaluate the current status of each activity. You must distinguish between these three variants:Â Â Â
- Value-adding activityÂ
- Non-value-adding but avoidable activityÂ
- Non-value-adding, unavoidable activityÂ
The goal is to expand the value-adding activities and reduce the non-value-adding activities. In addition, all avoidable activities without value creation should be eliminated along the entire value chain.Â
3. Implement the Flow Principle - Optimizing the Entire Throughput
The flow principle refers to a holistic approach. This is necessary because the product value is created by activities along the entire value chain. You must always keep an eye on the activities of the entire value creation process and not just individual sections. The goal is to ensure a continuous flow of activities by reducing inventory levels, defects, delays, and downtime. To achieve this goal, you may need to completely resynchronize or reorder entire process sections and their sequence.Â
4. Pull, Not Push - The Customer Determines the Work Rhythm
In the past, activities in manufacturing were oriented towards maximum machine utilization. This is known as the Push principle. The Lean concept, however, goes in a different direction and focuses on the Pull principle. In practice, this means: The actual customer demand is the decisive criterion, while capacity utilization is no longer a priority. The control of manufacturing processes and the corresponding activities is therefore not based on forecasts, but always depends on the customer’s needs or the customer’s specifications.Â
5. Kaizen - The Pursuit of Perfection
This fifth Lean principle essentially represents the overarching goal. The first four principles serve as the basis for achieving the respective goal. Kaizen is the Japanese term for this pursuit of perfection. The basic idea here is that there is always something that can be improved. Kaizen, therefore, aims to continuously question and improve projects, processes, and products. You can then interpret the resulting continuous improvement process as the pursuit of perfection.Â
Lean Project Management - These Tools and Techniques are Particularly Popular
Kanban
This method is used to ensure efficient control of workflows. For this, precise and reliable information transfer of material requirements in the respective project and manufacturing stages is necessary. This way, a lower inventory level can be achieved. The Kanban principle is used in various forms (single-card and multi-card system) and finds application in all areas of the company.Â
Scrum
In this agile project management method, so-called Sprints are used in the form of iterative cycles. Teams can then plan and prioritize their tasks as needed within these Sprints. In addition, complex projects can be broken down into smaller and more manageable subareas or tasks using the Scrum project management method.Â
Extreme Programming
This method is mainly used in software development. A defining feature is the cyclical approach at all steps of the development process. The steps are always performed at a certain pace. Within the cycles, the project team defines the respective requirements together with the customer, resulting in active customer involvement.Â
Six Sigma
This process improvement method is to be understood as statistical quality control. It aims to reduce deviations from the mean in processes and projects as much as possible. This also simultaneously reduces the error rate. Six Sigma follows a mathematical approach. Project processes are thus expressed as a mathematical function. The projects are given a fixed structure according to the DMAIC scheme: Define, Measure, Analyze, Improve, Control.Â
Value Stream Mapping
Value stream analysis or mapping is another approach in Lean Project Management to minimize waste and optimize value creation. Here, the focus is on customer-oriented process optimization. Companies or project managers use Value Stream Mapping to scrutinize their own production processes to assess the quality of the processes. This way, weaknesses and potential improvements in the value chain can be identified. The value creation refers to the value that a product gains for the customer at each project step.Â
Kaizen
Kaizen, as it is called, represents a method for the continuous, incremental optimization of processes. The applied methodology functions in Lean Management as the basic principle of continuous improvements.Â
Conclusion
Using the five principles of Lean Management, it is possible to establish a process with minimal or even no waste. The starting point is always the actual customer requirements. The Flow and Pull principles represent the two key elements for creating an optimal value creation process.Â
The Pull principle triggers value creation and prevents overproduction, while the Flow principle focuses on the required activities and their associated parameters (location, duration, dependencies, etc.). The overarching goal is ultimately represented by the pursuit of perfection (Kaizen). This is synonymous with a continuous improvement process.Â
In the context of project work, Lean Project Management stands for eliminating non-value–adding activities or elements and simultaneously creating additional value in each project phase. Lean Project Management is one of the agile methods.Â
The foundation for Lean Project Management was laid in the 1950s by then Toyota production manager Taiichi Ohno. He introduced the five Lean principles, thereby changing Toyota’s previous production strategy and ultimately the entire automotive industry. Through further developments and adaptations, the principles can also be applied in the project area. The first publicly known ambitions in this direction emerged in the late 1980s.Â
Lean Project Management is based on a total of 5 core principles:Â
- Focus on the customer and the customer perspective
- Identification of the value stream to expand value-adding activities and reduce non-value-adding activities
- Optimization of the entire throughput or all project and process steps (Flow principle)
- Control of manufacturing processes and individual activities is based on customer needs or customer specifications
- The pursuit of perfection is documented through a continuous improvement process